Un système pour une presse universelle économique
Comment concevoir et produire une gamme de presses de moyenne puissance défiant toute concurrence en termes de prix, de technologie et d’économies d’énergie ? Dieffenbacher, le fabricant leader de presses, a trouvé la solution en utilisant l’hydraulique industrielle de pointe de Bosch Rexroth.
Performances excellentes, prix imbattable : avec cette promesse, le fabricant de machines et de systèmes Dieffenbacher soutient les entreprises artisanales et les petits ateliers, mais aussi les industriels à la recherche d’une solution économique pour le formage de composants métalliques et composites. Une presse ultra-polyvalente pour des efforts de 1 000 à 10 000 kN produite à un coût suffisamment économique pour s’imposer face à la concurrence internationale : le constructeur nous explique comment il a réussi ce tour de force.
Un entraînement modulaire économe en énergie pour la gamme TailoredPress
Nous voulions fabriquer une presse adaptée aux besoins de demain à partir de systèmes standards modulables en effort, en volume et en taille de tablier et de vérin. Nous souhaitions également une haute performance énergétique. Bosch Rexroth répondait à ces deux critères. Nous avons donc conçu conjointement un concept d’entraînement modulaire qu’ils ont finalement produit pour nous.
Initier une technologie de presse plus durable
Dieffenbacher fait partie des grands constructeurs de presses mais aussi de systèmes complets pour le façonnage et le recyclage du bois. L’entreprise familiale, dirigée aujourd’hui par la cinquième génération et basée à Eppigen en Allemagne, propose de nombreuses solutions innovantes en matière de sobriété énergétique. Dieffenbacher s’engage ainsi à réduire ses propres émissions de gaz à effet de serre sur son site d’Eppingen de 50% d’ici 2030. La seconde mesure de sa stratégie en faveur du développement durable vise à fabriquer des presses aussi économes que possible en énergie.
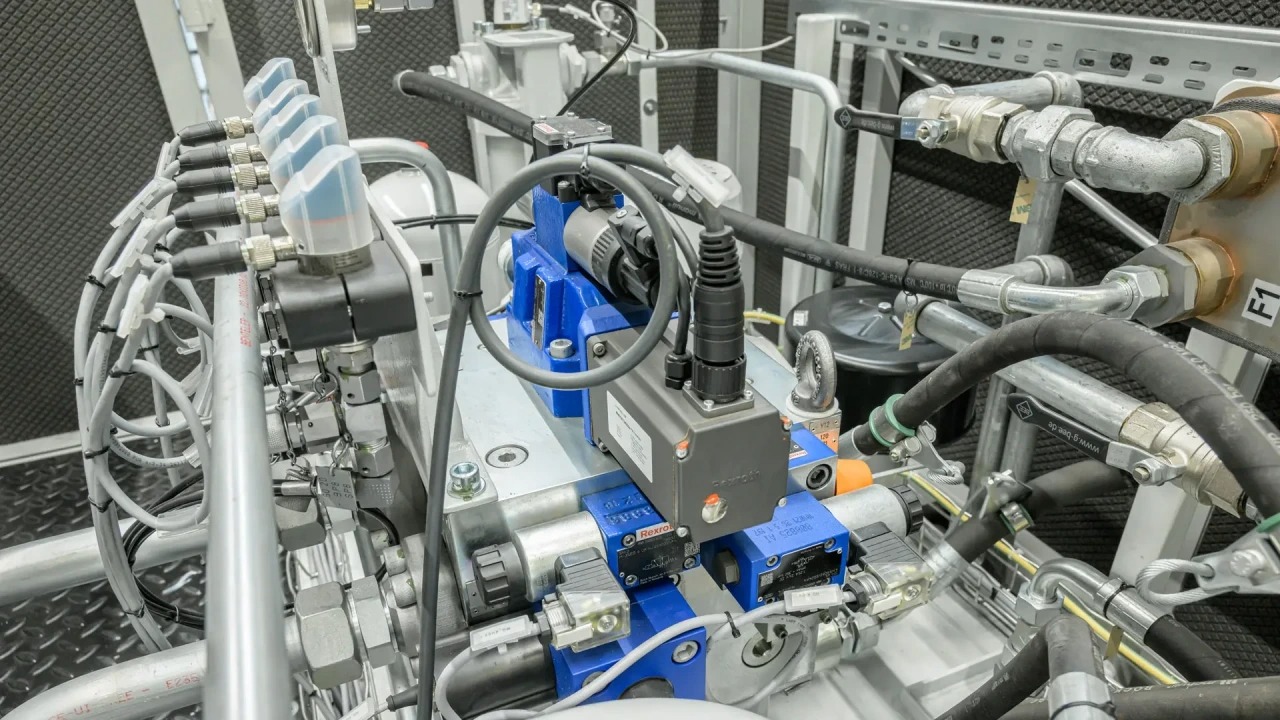
Technologie, fabrication et service : des critères déterminants en faveur de Bosch Rexroth
Le concept principal exigeait que le module d’entraînement de la gamme TailoredPress utilise une majorité de composants standards. Au-delà du concept d’énergie à la demande avec l’entraînement à vitesse variable, la technologie de pointe dans les pompes et le savoir-faire reconnu de Bosch Rexroth comme maître d’œuvre ont joué en sa faveur.
Le site de production partagé à Brno en République Tchèque renforce encore la coopération. A moins de deux kilomètres de l’usine Rexroth, Dieffenbacher peut monter les modules d’entraînement préassemblés directement sur la machine.
Bosch Rexroth a une excellente réputation mondiale dans les applications de presse. L’entreprise est championne en matière de technologie et a une image de stabilité et d’expertise.
Le concept d’entraînement modulaire
Le concept d’entraînement modulaire permet au constructeur de proposer facilement la TailoredPress en plusieurs plages de puissance et de vitesse. Par exemple, une version de 500 tonnes peut aisément être upgradée en vitesse avec un maintien parallèle actif à grande vitesse pour des épaisseurs de pièce précises et une qualité supérieure en utilisant un autre calibre de pompe. L’ensemble des services s’appuient sur la gamme de pompes de Bosch Rexroth capable de couvrir différents besoins. C’est ce qui permet de rationaliser les processus sur toute la durée de vie de la machine, de l’ingénierie et du stockage jusqu’à la maintenance. D’autres versions avec coussins de presse peuvent également être réalisées rapidement avec ce système modulaire.
Puissance à la demande : des débits volumétriques adaptés au besoin
L’entraînement principal utilise des pompes à pistons axiaux A4VSO de différentes tailles avec contrôle électronique numérique HS5, ainsi qu’un bloc hydraulique pour presse IH04. Ce dernier est doté d’un concept de sécurité et fourni avec un certificat de test pour le niveau de performance Pl e catégorie 4 selon les normes DIN EN ISO 16092-3 et DIN EN 289. Le circuit de régulation, de filtration et de refroidissement à eau est équipé d’un bloc de commande multi-embase et d’un groupe moto-pompe avec la pompe à pistons axiaux A10VSO. La fourniture de Bosch Rexroth comprend également une centrale hydraulique à régulation de vitesse adaptée à chaque type de presse.
Le concept d’entraînement électrohydraulique génère un débit volumétrique en fonction de la demande, d’un côté via l’angle d’inclinaison de la pompe et de l’autre, via la vitesse du moteur électrique. Ceci permet à la pompe de délivrer une puissance 1,5 fois plus élevée si nécessaire. Le contrôle électronique numérique ajuste précisément le débit volumétrique à chaque étape du process. Lorsqu’aucune puissance n’est requise, les pompes passent en mode veille afin que la TailoredPress ne consomme quasiment pas d’énergie en phase d’attente.
Jusqu’à 70 % d’économies d’énergie
Par rapport à l’entraînement conventionnel à vitesse constante, l’électrohydraulique contrôlée de façon optimale permet d’économiser environ 50 % de l’énergie consommée auparavant. En association avec une charge de batterie d’accumulateur, le potentiel augmente à 70 %. La TailoredPress à entraînement direct ajuste automatiquement la pression de charge de l’accumulateur hydraulique au process de formage programmé. Le système est transparent pour les opérateurs. Les forces, la course et les paramètres du vérin sont réglés comme d’habitude et les vitesses respectives sont calculées en arrière-plan.
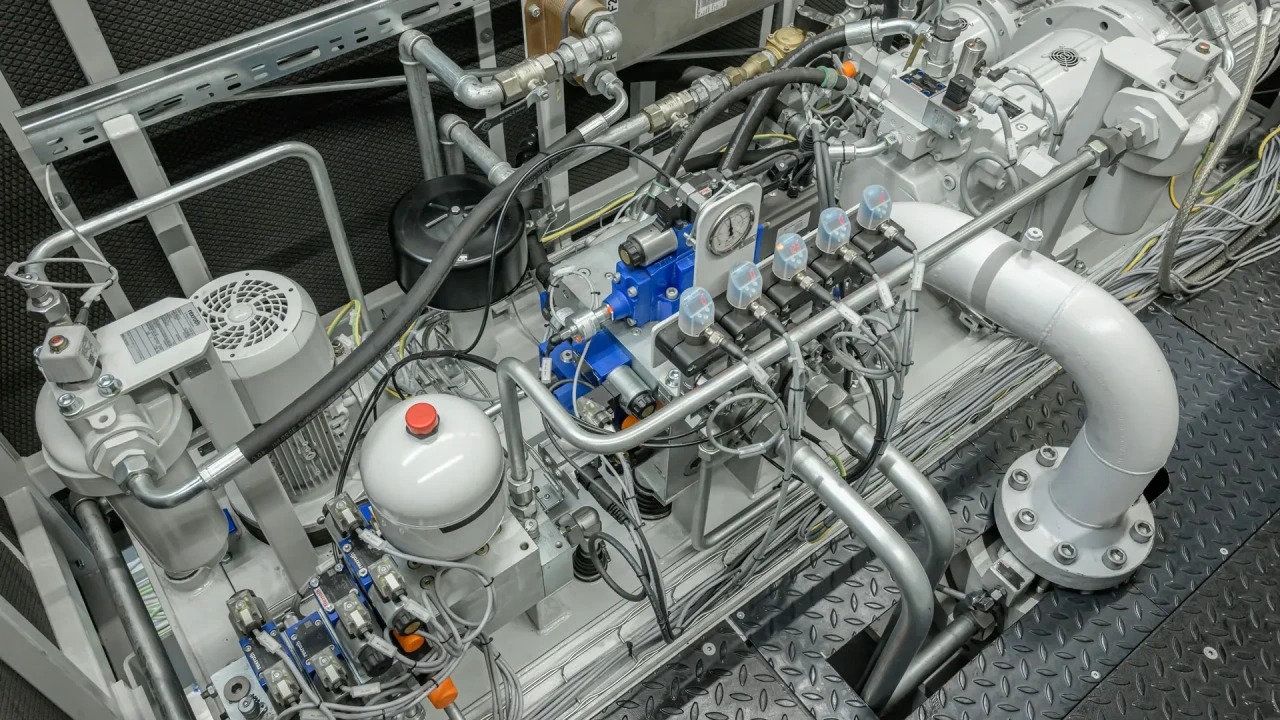
Maintenance facilitée avec la digitalisation de bout en bout
Le nouveau concept d’entraînement est également avantageux en termes de digitalisation. Les interfaces intégrées permettent à Dieffenbacher d’inclure sa plateforme digitale EVORIS à son offre de machines d’entrée de gamme. Avec la TailoredPress, ses clients bénéficient ainsi de services en ligne innovants comme la maintenance à distance, la surveillance d’état ou encore l’analyse fondée sur les données pour l’amélioration de leurs process ou pour la maintenance prédictive. Le constructeur peut quant à lui standardiser son service et gagner en réactivité dans le monde entier.
En plus de l’efficacité énergétique et de la digitalisation, cette technologie d’entraînement est remarquable de par sa compacité et le faible niveau sonore. Avec pas plus de 70 dbA, elle est bien en deçà de nos exigences de 80 dbA maximum.
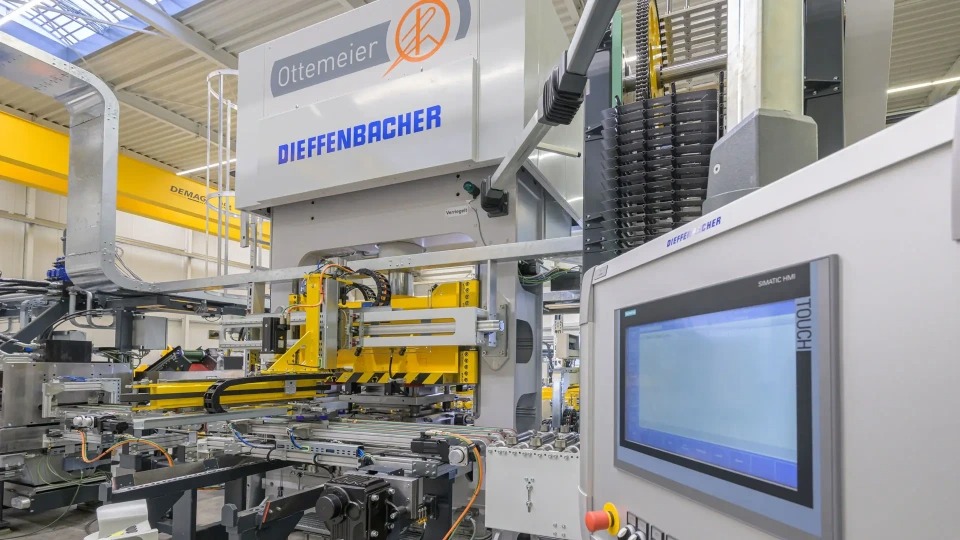
Une technologie d’entraînement aussi économique pour le retrofit
Les nombreuses améliorations obtenues poussent Dieffenbacher à étendre le concept d’entraînement de Bosch Rexroth aux projets de retrofit. Les mesures comparatives effectuées dans ce domaine montrent que l’entraînement à vitesse variable génère de 30 à 50% d’économies d’énergie selon le cycle.
A lui seul, le mode veille lors des phases d’attente réduit les coûts d’électricité et les émissions de CO2 indirectes de 20% en moyenne. Grâce à cet entraînement de nouvelle génération, nous sommes en mesure de proposer un concept de presse durable à un coût particulièrement attractif avec un retour sur investissement rapide. Cette collaboration a bénéficié d’un engagement et d’une offre orientée solution à tous les niveaux : conception, mise en service, production, support et approvisionnement de pièces de rechange. Toutes les exigences de performance ont été remplies dans la mesure du possible.
Nous avons intégré la Tailored Press à une ligne automatisée. Puis nous l’avons soumise à des tests intensifs. L’électrohydraulique à contrôle numérique a un fonctionnement très silencieux et génère la juste puissance requise pour chaque process. Notre client réalise ainsi une économie d’énergie et une réduction des émissions de CO2 de 50% par rapport aux entraînements conventionnels