Visser sous tension sans manquer un seul boulon !
Comment visser les batteries des véhicules électriques de manière fiable et efficace ?
Les batteries des véhicules électriques et hybrides doivent être vissées sous tension. Étant donné que les erreurs de montage présentent un risque pour la santé des ouvriers, le fonctionnement du véhicule et son système de sécurité, la législation prévoit un suivi obligatoire et une documentation stricte du processus.
Quelles solutions l’Industrie 4.0 propose-t-elle pour les liaisons vissées pendant la production et l’entretien courant, qui soient à la fois économiques et conformes aux normes ?
Plusieurs centaines de boulons par batterie
L’e-mobilité gagne du terrain lentement, mais sûrement. On estime que près de 20 millions de véhicules hybrides et électriques seront produits en 2025. Les responsables de production et de service après-vente sont invités à préparer leurs chaînes de production et leurs ateliers de réparation en conséquence. Au cours des années à venir, un grand nombre de batteries seront assemblées avec plusieurs centaines de boulons, selon les modèles, et auront un impact majeur sur la puissance, l’autonomie, la durée de vie et la sécurité des véhicules, en particulier.
Si un élément ne joue pas son rôle pendant la conduite, les personnes et l’environnement sont en danger. Par conséquent, conformément à la norme VDI/VDE 2862, les fournisseurs et constructeurs doivent surveiller précisément chaque fixation essentielle à la sécurité et archiver les données documentées pendant dix ans. Beaucoup de gérants veulent savoir comment réaliser la transition de manière rentable et efficace en production et dans le service après-vente, tout en garantissant la qualité du processus.
Assemblage de batteries complexes dans l’usine Bosch à Bamberg. La boulonneuse intelligente avec capteurs intégrés, permet d’éviter les erreurs et les rappels qui en découlent qui sont coûteux.
Le montage sous tension exige des concepts de sécurité entièrement nouveaux
Une batterie est un système complexe comprenant un contrôleur, des pièces formant un logement et de nombreux modules de piles composés d’éléments aux ions de lithium, qui arrivent de l’usine partiellement chargés. Même les réparations, par exemple, le remplacement d’un module, sont généralement effectuées sous tension. Un court-circuit à 400 ou 600 volts pourrait être mortel.
L’utilisation d’outils de vissage manuels ayant un cordon d’alimentation présente le risque de transfert involontaire du potentiel électrique vers des pièces métalliques conductrices, du boulon à la visseuse, puis au contrôleur. Bien entendu, cela représente également un risque considérable pour l’ouvrier qui actionne la visseuse manuelle. Afin d’éviter les blessures, les dégâts environnementaux et la responsabilité du fait du produit, sans pour autant mettre en péril la rentabilité, les industriels ont besoin de solutions de vissage fiables, intelligentes et évolutives, capables d’enregistrer et de transmettre les données sans fil.
Un système complet : intelligent, sans fil et sécurisé
Une solution tout-en-un de ce type, qui permet aux fournisseurs et les constructeurs de respecter facilement les exigences de la norme VDI/VDE 2862 tout en assurant la sécurité maximale des ouvriers, a été testée pendant plusieurs années sur la chaîne de production des batteries de Bosch Rexroth et finalement mise sur le marché. Elle associe une visseuse sans fil Nexo à l’isolation protectrice NXAP030/NXPP012, spécialement conçue pour l’assemblage des batteries. L’ouvrier est protégé d’un placement accidentel de la visseuse sur des pièces conductrices de la batterie, mais aussi du transfert de tension dans la visseuse. L’isolation en question fonctionne jusqu’à 800 V, ce qui est confirmé par la certification de Dekra. Elle empêche également les vêtements de se prendre dans l’entraînement de sortie.
La couche isolante protège les ouvriers des chocs életriques : dans le montage de batteries, des tensions de plus de 400 volts peuvent être présentes. Les précautions doivent être prises à partir de 48 volts
Un concentré d’expertise technique
Rexroth a tiré parti de plus de 30 années d’expertise en technologie de vissage pour concevoir la visseuse intelligente Nexo sans fil. En 1982, l’entreprise a lancé le tout premier système de vissage électrique au monde, équipé d’un organe électronique d’arrêt de la vitesse d’entraînement. Au cours des dix années suivantes sont apparus le premier système de vissage à programmation souple des étapes, puis le premier système de vissage entièrement numérique.
La première visseuse manuelle numérique a vu le jour exactement 20 ans avant la Nexo. La capacité multivoie et la logique intégrée de cette technologie innovante sont toujours d’actualité. Le dernier jalon en date est le logiciel Process Quality Manager, une solution née de la collaboration entre Bosch Rexroth et Bosch Software Innovations, qui utilise l’analyse des données massives pour détecter les écarts au sein des processus de production.
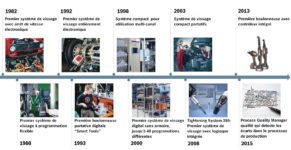
Un vissage fiable dans l’Industrie 4.0
En tant qu’utilisateur, Rexroth applique également son expertise à l’Industrie 4.0. Puisqu’elle possède une unité de commande entièrement intégrée, la visseuse Nexo s’insère dans le réseau des salles de production sans matériel supplémentaire et communique directement avec la commande de la chaîne et le serveur d’archivage. Le logiciel sur Internet fournit un accès aux données quel que soit le lieu de connexion, depuis un PC ou un appareil intelligent.
Grâce à son scanner de code-barre intégré, la visseuse sans fil peut également identifier les pièces correspondantes et guider précisément l’ouvrier pendant tout le processus d’assemblage. Si la connexion sans fil est perdue, l’appareil conserve temporairement les données de vissage dans un registre tampon et les transmet automatiquement une fois la connexion rétablie. Avec l’intelligence décentralisée, la connectivité, le recueil intégré des données et la commande de processus ciblée jusqu’à une taille de lot se limitant à un exemplaire, la visseuse sans fil Nexo remplit tous les critères de l’Industrie 4.0.
Le mariage des normes VDI/VDE 2862 et de l’efficacité
Conformément à l’obligation de suivi et de documentation des liaisons vissées critiques pour la sécurité, le couple et l’angle de rotation doivent être mesurés directement sur la visseuse, ce qui est par exemple possible avec des capteurs. Une mesure indirecte par le biais du courant consommé est suffisante. Pour chaque processus de vissage, le système de complet de capteurs de la Nexo produit jusqu’à quatre pages A4 DIN de données, fournies au format open source JSON (JavaScript Object Notation). Le responsable du processus reçoit un graphique exact pour analyser rapidement chaque cas de vissage.
La comparaison avec le processus optimal permet de détecter bien plus d’erreurs que ce qu’exige la législation. Dans l’assemblage de batteries, par exemple, il est possible de détecter un câble incorrect en vissant le collier de serrage, grâce à des paramètres prédéfinis du programme de vissage. Les boulons incorrects et les rondelles manquantes ou en double sont d’autres exemples de défauts qui peuvent être décelés pendant le processus.
Un guidage précis de l’opérateur au lieu d’une remise en fabrication coûteuse
La taille de la base de données détermine également l’efficacité d’une stratégie de prévention des défauts et d’évitement des remises en fabrication. Finalement, l’assemblage des batteries suit une séquence précise, dans laquelle aucune liaison vissée ne peut être oubliée ou défaillante.
Afin de contrôler le nombre de liaisons vissées du processus et d’identifier les liaisons anormales, un programme distinct peut être créé pour chaque cas de vissage, qui est à son tour divisé en 12 étapes maximum, y compris le dévissage et le revissage. L’ouvrier reçoit des consignes précises sur un terminal d’affichage, avec une solution de localisation. Un point bleu indique par exemple à l’écran le prochain emplacement de vissage. Une fois le vissage effectué, le point devient vert.
Il est également possible d’interrompre une séquence de vissage. L’emplacement de vissage correspondant est sauvegardé et s’affiche lorsque la tâche reprend. Si la visseuse ne se trouve pas au bon endroit, l’approbation n’est pas donnée. La localisation de la visseuse peut faire appel à une triangulation entre l’émetteur et le récepteur, à une caméra ou des ultrasons, voire une combinaison des deux. Dans les systèmes stationnaires, la visseuse peut être localisée avec une précision de 10 mm.
Conclusion : un montage en rattrapage « zéro défaut »
Avec les systèmes intelligents et complets assurant un vissage fiable, les constructeurs automobiles, fournisseurs et prestataires de service peuvent protéger efficacement la santé de leurs travailleurs, améliorer la productivité en allant au-delà des obligations de suivi et de documentation et préserver et optimiser la qualité du processus à long terme.
De plus, les séquences complexes d’assemblage des batteries de voiture électrique ou hybride peuvent être conçues non seulement de manière à respecter les normes, mais aussi de manière à être efficaces et dépourvues d’erreurs.
Pour aller plus loin :
Le poste de travail interactif numérique : placer l’Homme au cœur de l’Industrie 4.0 !