La passerelle d’IoT recueille les données des capteurs
L’élément essentiel à la collecte et au transfert des données est la passerelle d’IoT, IoT Gateway, développée par Bosch Rexroth, qui recueille des données, notamment la différence de pression entre l’amont et l’aval du filtre, auprès de capteurs installés en rattrapage pour donner un idée du niveau de contamination de la cartouche filtrante. D’autres capteurs détectent le diamètre et le nombre des particules, surveillent la température et enregistrent la teneur en eau dissoute de l’huile hydraulique.
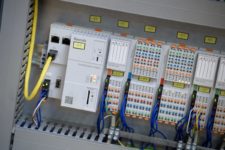
Prêt à l’emploi : connecté en quatre heures seulement
La méthode classique de modernisation du banc d’essai – incluant la connexion des capteurs, les interfaces et la programmation classique des automates industriels programmables (API) – aurait demandé une semaine à l’équipe de spécialistes. La mise en œuvre simplifiée à l’aide d’IoT Gateway a réduit ce délai à une demi-journée. Le logiciel de configuration sur Internet ne nécessite aucune connaissance en programmation. Il suffit de saisir quelques paramètres et de faire quelques vérifications. Finalement, le travail d’ingénierie requis pour la modernisation du banc d’essai a été réduit de 90 %.
IoT Gateway et Production Performance Manager (PPM)
Le matériel d’IoT Gateway s’appuie sur un contrôleur XM21 de Bosch Rexroth destiné aux applications industrielles. Ce matériel, dont la fiabilité et la durabilité sont certifiés, est un système ouvert qui prend en charge un grand nombre de capteurs et de sources de données de divers fabricants, tels que des capteurs analogiques et numériques, des contrôleurs externes ou des sources de données basées sur l’OPC UA.
À Hombourg, IoT Gateway envoie les données des capteurs, collectées et traduites en interne, à un serveur sur lequel est installé Production Performance Manager (PPM), le système d’information et d’analyse de la production de Bosch Software Innovations. Ce système obtient presque en temps réel les données de la production et des machines auprès du banc d’essai connecté ; il fusionne les informations en une seule visualisation et transmet les événements spécifiés à des personnes prédéfinies.